Scottish Steelworks History
Description of Clydebridge Steelworks
Contents:
​
Original 1887 Works Layout
The Engineering Review Supplement, December 20th, 1894.
Description of Clydebridge in the 1970s
​
Original 1887 Works Layout
The earliest record I have found relating to Clydebridge is a quotation, dated 16th November 1885, from Miller and Co, Coatbridge to supply a plate mill, cogging mill, and steam engines to drive the mills, plus a hot bloom shear and a plate shear. This is addressed to Hugh Neilston, Barlanark House, Bothwell and is for a grand total of £16,750. In the event, only the plate shear was accepted from this quotation, after its price had been reduced from £1250 to £1200.
The original works comprised the following plant:
​
-
four (shortly afterwards increased to six) acid lined open hearth furnaces, of nominal capacity 25 tons;
-
a battery of gas producers from Hanna Donald & Wilson (£2100);
-
ingot reheating furnaces;
-
a 28½ inch slab cogging mill from R B Tennant (£4800 including plate mill), and non-condensing steam engine, from Lamberton & Co;
-
slab shears from Grant Richie & Co, of Kilmarnock (£2050);
-
slab reheating furnaces;
-
two off, two stand, reversing plate mills, (a heavy plate mill and a light plate mill) with rolls 29 in diameter by 8ft long, driven by non-condensing steam engines, one a 42 inch diameter cylinder and the other a 38 inch diameter cylinder, by 5 ft stroke, from Lamberton & Co (only No 1 plate mill was in place when the works opened, No2 plate mill was installed sometime between 1887 and 1894);
-
plate shears from Miller & Co (£1200);
-
a battery of Lancashire boilers, 28ft by 7ft 6 ins, from Penman & Co (£329 each).
In 1907 a further two 50 ton furnaces were added and No3 heavy plate mill (42 inch diameter rolls by 13ft 6 in long) was installed. The plant continued working with steam drives for some time, but after the formation of the Clyde Valley Electrical Power Company Ltd, and the opening of the Motherwell supply station, current for some of the services was taken from that company and a number of cranes and slab charging machines were converted for electrical driving.
[Note: Mills for rolling ingots into slabs are called Cogging Mills in the UK but Slabbing Mills in the USA. The first Slabbing Mill in the USA was at Cambria in 1871, the first in the UK was at Blochairn in 1884. Previously ingots were converted into slabs using Slabbing Hammers (i.e. a Naysmith type Steam Hammer), Ref Colvilles Magazine February 1925, Rolling Mills by T. MacKenzie M.I.Mech.E.]
27 May 1887 - From "Iron & Coal Trades Review"
​
Clydebridge Steel Works - At last there is something definite to report regarding the new steel-making concern that has been so often spoken of in Glasgow. The principal movers in the concern are Messrs. Walter and Hugh Neilson, sons of the late Mr. William Neilson, of Mossend, but there are associated with them a sufficient number of partners to make up a private limited company.
​
A site, extending to about 20 acres, has been secured for the works, near Cambuslang, three or four miles from Glasgow, close to the spot where the railway bridge crosses the Clyde at Clyde Iron Works, and railway connection from the Caledonian Railway Company's system has now been led into the site on which the works are to be erected.
​
The plans have been so well brought out that it is quite "on the cards" that finished steel will be turned out before the close of the present year. At first the manufacturing operations will start with four Siemens' steel-melting furnaces, each capable of making 25 tons of steel at a melting, and these will be followed by others as circumstances may warrant.
​
Arrangements are far advanced in respect of the machinery that is to be laid down in the new works. There will not be a steam hammer, but instead a powerful cogging mill will be erected for dealing with the ingots of steel prior to being rolled out into finished goods. It is reported on excellent authority that the intention at first is to limit the marketable products to plates for shipbuilding, boilermaking, and bridge-building purposes; but it is just possible that by-and-by the output of the works at Clydebridge may include finished steel in other forms.
​
Most of the machinery is being made by well-known firms in the Coatbridge district, and the engineer who is planning it all is Mr. Thomas Williamson, who has had an extensive and varied experience in connection with steel works in Scotland, England and Wales; and in respect of his professional skills he takes high rank amongst his contemporaries.
​
Early Days at Clydebridge
by " Le Carbone" - from Colvilles Magazine February; 1920 Page 32-33
Originally laid down in 1887 on the top of an old slag hill, the refuse from Clyde Ironworks, by Messrs. Hugh and Walter Neilson of Mossend, the Clydebridge Steel Works have given employment during the past 30 odd years to hundreds of workers in and around Cambuslang and Rutherglen. Associated with the brothers Neilson in the formation of the old Clydebridge Steel Company was Mr.J.B. Paton, father of our present Assistant Manager.
​
The Plant, was designed by Mr. Thomas Williamson, a Glasgow engineer, and managed by Mr. Hugh Neilson, consisted of five 25 ton Siemens' Open Hearth Acid process Melting Furnaces, No. 1 Cogging Mill and No. 1 Plate Mill all the brickwork of which was built under the supervision of Mr. Joe Leighton of Mossend. No. 1 Cogging Mill and No.1 Plate Mill were erected by Mr. John M'Lean, of Messrs. Lamberton & Co., Coatbridge, who contracted the work to Mr. Williamson's design and specification.
​
Note, from Colvilles and the Scottish Steel Industry by Peter Payne, and The Engineering Review, 1894: Thomas Williamson was trained by Tulloch & Denny at Dumbarton and subsequently worked at Neilson's Locomotive Works, Dubs, and Rowan's Marine Engineering Works. He was appointed works manager at the Hallside works of the Steel Company of Scotland in 1875 and was responsible for the conversion of Blochairn to steel-making when that works was acquired by the Steel Company in 1879. Before becoming Engineer to the Glasgow Iron & Steel Company at Wishaw, he designed and superintended the erection of Clydebridge works and those of John Spencer & Co at Newburn, Newcastle-on-Tyne. He probably had more experience of designing steel works than any engineer in the country.
​
​
​
​
Mr Thomas Williamson, in 1894
​
The first Works Engineer was Mr. Andrew Gillespie of Mossend, an uncle of Mr. James Gillespie, now Chief Engineer for David Colville & Sons Ltd., while Mr. Alexander Allan, father of Mr. George H. Allan of our present Office Staff, had charge of all the Steam Plant, including a main range of six Penman Boilers. While the Works were in course of erection there arrived, to learn the art of steel making, two youths Mr. Robert B. Paton, now Assistant Manager, and Mr. David M. Maclay, now a Director and the General Works Manager of Messrs. Colville.
​
Letter from D B Barrie, Rutherglen, in Colvilles Magazine March 1920
​
In last months magazine, I noticed a statement by "Le Carbone", In Early Days at Clydebridge, to the effect that Mr John M'Lean of Messers Lamberton & Co, Coatbridge, erected No1 Cogging Mill and No1 Plate mill. I beg to state, however, that it was Messers R B Tennant, Whifflet Foundry, Coatbridge who erected the above. Mr M'Lean had charge of the setting down of the engines for driving the same, built by Sunnyside Engine Works (Messers Lamberton & Co). Some time later Mr M'Lean had charge of erecting No2 Plate Mill, being then Foreman Engineer for the Clydebridge Steel Co Ltd.
​
In those early days, before the introduction of electricity as a motive power, the methods of production were somewhat crude. All the furnaces were hand charged, the Ingots from the charges being handled by means of a 15 ton Portable Steam Crane, which also did duty in pushing the ladle carriage along the casting pit. The Ingots cast at that time weighed from 25 to 60 cwt and were taken from the pit and dropped down on a sand bed, from where they were lifted by a 10 ton Steam Crane operating in front of the Cogging Mill. The heating arrangement at the Cogging Mill consisted of two Vertical Reheating Furnaces, the underground Live Soaker not then being in vogue. From the sand bed, the site of which is now occupied by Dead Soakers, the Ingots were conveyed by the Portable Steam Crane and placed on the sill of the furnace, to be later worked into a suitable position to ensure their receiving the proper heat. When sufficiently hot for rolling, they were drawn from the furnace, the Ingot being gripped by a huge pair of tongs, to which the crane chain was attached, and placed on a roller rack. There were three live rollers on either side of this Mill; while the screws for setting the rolls were operated by a small horizontal steam engine direct coupled to the worm-gear.
​
At the Cogging Mill, after rolling, the slab was cut into lengths by Steam Shears or Guillotine, loaded on iron bogies by a Steam Derrick, and drawn by squads of men to the Plate Mill Heating Furnaces. Here were two furnaces, in front of which was a hydraulic cylinder, termed in the vernacular "The Polisman." In charging these furnaces, the, loaded bogie was run alongside the sill, the slabs being levered off into the furnace with "chippers" or crowbars. The slabs, when heated to the necessary rolling temperature, were drawn out again on to the iron bogie by the same laborious method as adopted at the Cogging Mill, the hydraulic cylinder serving the purpose of the Steam Crane. There were no roller racks at the Plate Mill, their place being taken by steel plates, which had ribs cast on them to serve the purpose of heels or fulcrums, whereby the workmen were enabled to lever the material forward towards the Rolls. The screws for this Mill were operated by a small horizontal steam engine, erected on a bracket on the side of the Mill housing. The change over from soft to hard rolls was effected by the use of bogies, the screws for the finishing rolls being hand operated. In addition, there was a loose roller which served to support the end of the plate during rolling.
​
Since that time the Works have gradually extended; in later years a large tonnage of plates manufactured here being used in the construction of the Mauretania [launched Swan, Hunter & Wigham Richardson, Wallsend-On-Tyne 20 September 1906], The Empress of Ireland [launched Fairfields, Govan 27th January 1906], and many other large liners. Electricity from the Clyde Valley had been introduced and machinery and plant brought more up to date; and since Messrs. Colville purchased the Works in October 1915 a great transformation has been effected.
​
The Engineering Review Supplement, December 20th, 1894.
THE WORKS OF THE CLYDEBRIDGE STEEL COMPANY LTD.
These are among the most recent of the numerous establishments that have been constructed in the neighbourhood of Glasgow for the manufacture of open hearth steel. They were built in the year 1887, and they were not only constructed within a remarkably short period (having been at work within ten months of the ground being broken), but they were laid down at an unusually low cost. The situation of the works is admirably planned. They are on the main line of the Caledonian Railway, between Glasgow and Motherwell, on the coalfield, whence they draw cheap supplies of fuel, and within an easy distance of blast furnaces that furnish an ample supply of haematite pig iron at a comparatively low cost. The works were designed by Mr. Thomas Williamson, now the managing engineer to the works of the Glasgow Iron and Steel Company at Wishaw, whose portrait was given in the last issue of the ENGINEERING REVIEW. As originally constructed, the works had only four melting furnaces and one plate mill, but now there are nine melting furnaces and two plate mills, with all their usual accessories.
One of the points in respect of which the design and construction of Clydebridge Works differs from most others is the size of the furnaces and general strength and solidity of the plant employed. The melting furnaces, to begin with, are each of 40 tons capacity, and. it is no unusual thing for one of these furnaces to produce 50 ton charges.
​
It is still a moot point among open-hearth, steel producers and engineers whether there is much to be gained, on the whole, by furnaces of such large capacity. It is obvious that with a 40 ton furnace, you have less capital cost, and less labour for a given result than you would have with two 20 ton furnaces. On the other hand, however, you have certain countervailing disadvantages, not the least important of which is that when the furnace is laid off for repairs the work is altogether stopped for the time being, whereas in the case of the smaller furnaces the work is not suspended to anything like, the same extent.
​
At the Clydebridge works the melting plant appears to be designed with excellent judgment. The importance of economy of working has been studied in every detail. The charging bench, to begin with, is 50 ft. wide, so that the men employed in front of the furnaces have plenty of room to work, and this is of advantage in enabling them to do their several duties with more ease and facility. For each of the seven melting furnaces two men are employed in front, and these men have to handle, for the melting plant as a whole, about 20,000 tons of material per month of all kinds. The coal, ore, sand, &c., are delivered on to the charging platform from a siding that runs along the whole length of the line of furnaces. The tapping of the furnaces does not call for any special remark. The casting-pit is not immediately behind the furnaces, but at one end of the group, so that when the metal has been tapped into a ladle in the ordinary way it is carried by a locomotive crane along the casting-pit, where it is run into the ingot moulds. Both the casting ladles and the moulds vary greatly in size.
​
It is only a few years since the ladles were not generally adapted to carry more than 5 tons. Now, however, the ladles are in some cases capable of dealing with ten times that quantity. At the Clydebridge Steel Works one or two of the ladles can carry 50 tons of metal.
The ingot moulds are usually adapted to 5 ton ingots, which after having been "stripped," are conveyed by a locomotive crane to a range of soaking pits alongside, where they are left for about twenty-five minutes before being carried to the cogging rolls. These vertical underground furnaces or soaking pits are now very generally adopted in the steelworks of Scotland. They are found to be much more economical and readily handled than the old system of reheating furnace, which they have superseded. The pits at Clydebridge take twenty-four ingots of the largest size at one time. Heat is supplied to the pits by a special system of regenerators of the Siemens type built alongside. The ordinary type of furnace is used for heating ingots and raising steam.
​
The ingots which have to be rolled off into ship-plates, for the most part, are removed from the soaking-pits to the cogging mill, which is of a specially powerful type. This mill is driven by an ordinary high-pressure horizontal engine, made by Lamberton, of Coatbridge, with 38 in. cylinders and 5 ft. stroke, working at a pressure of 75 lb. The cogging rolls are provided with an ingot-tilter, like most of the other steelworks in the West of Scotland, so that, from the moment that the ingot is placed on the live rollers in front of the mill until it is reduced to the form of a slab, all the motions are perfectly automatic.
​
In their passage from the cogging to the plate mill, the slabs are taken to a powerful shears, where they are cut up into different lengths corresponding to the weight and dimensions of the plates to be produced. The usual size of the slabs is 36 in. by 10. The shears have 2-ft. nuts and 10-in. bolts. The machinery is all below ground, which gives ample room for the men to work, nothing being seen above but the shears proper.
​
The slab shears at Clydebridge is perhaps the most interesting mechanical feature of the works. It is capable of cutting hot steel blooms or slabs measuring 36 in. by 10 in. It has a stroke of 12 in. The motive power is provided by a pair of coupled engines having cylinders 26 in. in diameter by 24 in. stroke, which are supplied with steam at a pressure of 75 lb. on the square inch. These engines are arranged one at each side of the shears, and drive on to a crankshaft which carries the first motion pinions. These pinions and the whole of the gearing are in duplicate, there being a complete train at each side of the shears. The teeth are all of the helical type; the pinions are3 1/2 in pitch and have five teeth they are shrouded up to the pitch line and gear into similarly constructed wheels 5 ft. 5.7 in. in diameter by 9 in wide, with 59 teeth. The wheels are mounted on a countershaft of steel with. bearings 11 in. in diameter by 1 ft. 4 1/2 in. long. On this shaft are also two other pinions of 16 teeth, 4 1/2 in. pitch, 12 in. width, and 23 in. in diameter. These are also shrouded up to the pitch circle. They gear into the main spurwheels on the machine. These latter are 7 ft. 9.14 in. in. diameter by 4 1/2 in. pitch; they have 65 teeth, are 12 in. broad, and are 16 in. wide over the shrouds. The rims are of Siemens cast steel, and have male dovetails cast on for keying and wedging with steel and oak wedges on to the disc arms, which have female dovetails.
​
The throw shaft on which these wheels are mounted is made of mild steel, and has a throw of 6 in. It is 18 in. in diameter and is bossed up to 20 in. in diameter in the eyes of the main spur-wheels. The shear slide ram is of Siemens cast steel, and is fitted at the top end into the slide with a knuckle joint, and a 2 1/2 in. pin. The slide itself is of Siemens cast steel. It works against a fixed jaw, the stress being taken by two cast-iron columns, through each of which pass two forged Siemens steel bolts, fitted at each end with steel nuts.
​
The slab is carried up to the shears by a train of rollers worked by a pair of vertical engines, having cylinders 9 in. in diameter by 14 in stroke, geared 3 to 1. These engines are provided with link motion. They are coupled by gear to the roller gearing, so that either set of rollers at the back or the front of the shears may be worked independently of the other set. The rollers are 2 ft. 6 in. apart, 18 in. in diameter, and 2 in. thick. Each is fitted with a steel mitre wheel of 2 1/2 in. pitch and 5 in breadth, driven by a similar wheel of the side shaft.
This machine has been constructed and erected by Messrs Grant Ritchie & Co., of Kilmarnock, from the designs of Mr. Thomas Williamson, the then engineer to Messrs. Neilson, by whom the works were originated.
​
(Note: From Iron & Coal Trades Review 21 Oct 1887 - The Carron Company has just delivered to Messrs. Grant Ritchey, and Co., engineers, Kilmarnock, a casting forming the top frame of what is said to be the heaviest set of slab shears at present at work in this country. The casting weighs some 27 tons, is held down to the sole-plate with four 10-in. in diameter Siemens steel bolts, and has to withstand a strain of 1,500 tons. The machine will be capable of shearing a slab of steel 30-in. wide by 10-in. thick, and the power will be supplied by a pair of horizontal engines, 26-in. cylinders, and 24-in stroke, working with a boiler pressure of 100lb. per square in. One peculiarity of this machine is that the ram cuts from below in place of from above, as is the case in the usual type.
​
The plate mills commence operations, as a rule, on a 5-in slab and rolls it down, to a 3/4 inch plate in about fourteen passes. The mill is large enough to take in any ordinary size of plate, and works a high rate of speed and great smoothness. The rolls, which are of steel, are 29 in. diameter, and 8 ft. long. The mill is driven by a pair of engines, made by Messrs. Lamberton, Coatbridge, having 38 in. cylinder and one 42 in. cylinder and 5 ft. stroke. These and all the other engines on the works are equipped with a battery of. nine boilers, each 7.6 ft. by 28 ft., of the ordinary Cornish type, fitted with Galloway tubes, three on either side. A hydraulic, accumulator works the cranes, testing machines, and other accessory features of the works.
​
When the plates have been rolled they are sheared by two powerful machines supplied by Craig & Donald, of Johnstone, in Scotland, having a gap 37 in. wide, so that there is ample space in which to manipulate the plate under treatment. The shears can deal with ship plates of the largest size.
​
Another feature of the works is that the Siemens butterfly valve, which was formerly employed at the heating furnaces, has now been discarded in favour of the water valve, adopted at Barrow and some other works, which is fitted with four ports, and easily worked, the ports being reversed by a quarter turn.
​
The arrangements for loading the plates into wagons are excellent, the plates being moved from the bench on which they are laid after having been cut to the required dimensions, into the wagon on a lower level, by a travelling crane running parallel to the trucks.
As an instance of the resources of a modern establishment of this description, we may cite a case that actually happened quite recently. The Clydebridge Co. had been executing a contract for plates for the well known firm of Harland and Woolf, of Belfast. One day, about three o'clock in the afternoon, a telegram was received from the Belfast firm, intimating that they were in urgent want of a ship-plate which should be delivered next day. The plate was immediately put in hand, an ingot was heated, cogged, rolled and cut, and at five o'clock the finished plate left the works, in ample time to be delivered next morning at the ship-building yard at Belfast.
​
Glasgow Herald, 29 Oct 1912
​
We understand that proposals have been made lately to reopen Clydebridge Steel Works, which under an agreement with the Scotch Steelmasters Association were closed about five years ago when the trade was in a depressed state and have not since been in operation. A number of shipbuilders are associated with a scheme for restarting the works and in the event of its adoption by all the parties interested the plant will be put in service at the earliest possible moment.
​
Main Office - 1920
The main office, newly built, is described in the February 1920 edition of Colvilles Magazine:
​
The new office at Clydebridge is a substantial building two storeys in height, built of "Locharbrigs" red sandstone, all the floors being fireproof and covered with Dolomont. Situated on the south side of the Caledonian Railway, it faces the south west, the main entrance being at the south west corner. Entering by this door, there is a, Waiting Room on left and a Commissionaire's Room on right. The General Office is on the ground floor, facing the south, and is a large room well lit from both sides. The other rooms on the Ground Floor are the Works' Manager's Room, with Private Waiting Room opposite; Typists' and Comptometers Room, and the Pay Office, adjoining which is the new Time Office. Two large Lavatories are also situated on the ground floor.
​
The Staircase, open and well lighted, leads to the following rooms. The Laboratory, equipped with all necessary apparatus for analyses required in the manufacture of steel. The Telephone Exchange, situated between the Laboratory and the Drawing Office. This Office is provided with all modern requirements, including a room fitted with up to date apparatus for producing rapid prints of Drawings. The Cost Department on the north west side. A large Dining Room and Directors' Room on the north side.
​
A Servery between the Kitchen and Dining Room. The Kitchen, situated on the north east, with a special staircase from the outside, is provided with the latest electrical cooking range and other fittings, including an Electric Hot Plate and Oven.
​
The whole building is lit with electricity supplied from the Works Power Station, and heated throughout with hot water radiators from an "Ideal" sectional boiler. Another boiler of a smaller size supplies hot water for all domestic purposes.
​
Colvilles Magazine, January 1920 Pg 14
​
A most unfortunate mishap occurred at the new offices, just occupied, to our esteemed Master of Works, Mr John Wilson. Whilst in pursuance of his duties during the severe storm, on Thursday, 18 December 1919, he had occasion to go round outside one of the buildings, when a strong gale lifted him bodily and threw him against the wall causing severe facial injuries. With the assistance of Dr Hutchison, Cambuslang, his injuries were temporarily dressed, and he was removed home by motor to Motherwell. It was found that his forehead, lip and chin had to be stitched, the injuries being so severe. At the time of writing he is making fair recovery.
​
Description of Clydebridge in the 1970s
​
This description is from a leaflet for visitors to the works in the 1970's ( I have various other detailed technical descriptions written at earlier times but this describes the works at its peak).
​
Clydebridge Works, with its modern plate-producing plant covering an area of 140 acres, is situated at Cambuslang, about four miles from the centre of Glasgow -and just across the River Clyde from Clyde Iron Work. Founded in 1887 by the Clydebridge Steel Company, it was taken over by Colvilles in 1915 and during the First World War the principal product was shell billets for use with the famous French 75 mm field guns.
​
For many years Clydebridge Works has specialised in the manufacture of steel plate for structural engineering, shipbuilding, for heavy oil tanks and other large containers, and for armour plate. Many famous ships built on the Clyde, including the three Cunard Queen Liners, were built with plates rolled in these works.
​
The steelworks is closely integrated with Clyde Iron Works, about half a mile away, to which it is connected by a private railway and bridge across the river. Hot liquid iron is brought from Clyde Iron Works in rail-borne ladles, each carrying about 70 tons. The liquid iron is mixed with steel scrap, limestone, and special fluxes and other oxidising agents in a mixer furnace of 500 tons capacity, and then taken to three 150-ton fixed open hearth melting furnaces and three 300-ton basic open-hearth tilting furnaces. Finally the liquid steel is tapped from the furnaces into ladles of 140 tons capacity and then teemed into ingot moulds. The ingots thus made weigh up to 14 tons. The ingots are then slabbed and rolled into steel plates of various thicknesses and sizes according to the customers requirements.
​
Melting Shops
​
The 500-ton capacity mixer furnace mentioned above is known as a semi-active metal mixer, and it serves as a reservoir of hot liquid metal for the six open-hearth Siemens/
Maerz type furnaces which constitute the next process. The depth of liquid metal in the mixer is 6 feet, and it is maintained at a temperature of l,350oC by the combustion of heavy fuel oil. The mixer is filled with liquid pig iron (brought in rail-borne ladles from the blast furnaces at the Clyde Iron Works) and scrap steel, limestone, fluxes and oxidising materials. The silicon content of the liquid iron is thus reduced to the order of 0.5 or 0.6 per cent. The 70-ton capacity ladles in which the liquid pig iron is brought on rail-borne bogies are handled by 200-ton capacity overhead electric cranes. The ladles are hoisted over the mixer and the hot liquid iron is poured in, while the steel scrap and other materials are fed through the front doors of the mixer by special furnace charging machines.
​
The special advantage of the three 300-ton capacity tilting furnaces is that they can be rolled in either direction from the horizontal position to allow either slag to be poured off in one direction or steel tapped off in the other. This is carried out by means of a motor driven gear and rack mechanism.
​
The proportion of iron to scrap is determined by the availability and the economics of the use of scrap. Generally, the amount of scrap used on the tilting furnaces is about 75 per cent and about 40 per cent on the fixed furnaces.
​
All the furnaces at Clydebridge, both fixed and tilting, are fitted to supply their surplus heat to waste heat boilers which provide the works with a considerable proportion of its live steam requirements for the generation of electrical power which can be used within the works.
The steel is ready to be tapped from the furnace when the undesirable elements in it have been reduced to meet the desired specification and when the temperature of the steel is correct (about 160Q C). Tapping is done by opening a clay plug which is situated low down in the back of the furnace. The steel flows from the taphole over a brick lined channel into a ladle of 140 tons capacity suspended from an overhead crane. Certain alloys are added while the steel is pouring into the ladle. This is done both to cleanse the steel and to meet specific customer requirements. The steel is poured from the ladle into moulds set up on a train of cars. When the steel in the mould has solidified sufficiently the train is transferred to a bay where the moulds are removed by a crane and the ingots are charged to the soaking pits.
The Preheater
The preheater accommodates 14 ingot cars, each of which takes either three 7-ton or two 10-ton ingots. The preheater is controlled by a sequence of operations through limit switches, and the ingots are heated from cold to about 1,050oC before being charged into the soaking pits.
Soaking Pits
There are eight soaking pits for reheating the ingots to a suitable temperature before they are fed into the slabbing mill; six of these pits are used for normal working. The pits are of the end-fired regenerative type and are heated by a mixture of blast furnace and coke oven gas from Clyde Iron Works. Four of the soaking pits are automatically controlled from instrument panels, housed in a cabin facing each pit. These instruments record and control the gas and air flow and the pit pressure, and automaticallv control the pre-set soaking temperature.
The Slabbing Mill
This mill is of the reversing high-lift type, and was designed and built by the Engineering Division of Colvilles. The large-diameter rolls permit a maximum opening between the barrels of 54 inches, with future provision for still higher lift. Its purpose is to reduce the thickness of the ingots prior to passing them through the four high plate mill.
The slabs are lifted and carried by overhead crane and laid on stillages at the end of the bay. From there they are carried to a slab cooling area open at the north side and adjacent to the slab yard. After cooling the slabs are taken by heavy-duty fork-lift trucks to the deseaming area of the slab yard, where every slab is carefully inspected and surface defects are removed by oxy-propane torch. After deseaming the cooled slabs are assembled in the slab stockyard. As required the slabs are lifted by a semi-portal crane and placed on the feed table ready for charging into the pusher furnace.
The Pusher Furnaces
There are two continuous pusher furnaces, one capable of heating up to 65 tons per hour, the other 45 tons per hour.
These furnaces have three heating zones through which the slabs are progressively heated from cold to a temperature of 1280o C before reaching the output end. The heat is supplied by oil and coke oven gas, which is delivered through burners located in each zone. The hot waste gases are passed to a waste heat regeneration boiler, which ensures efficient utilisation. The slabs being heated in these furnaces are from 6 to 10 feet long, 30 to 40 inches wide and 5 to 12 inches thick.
.
After discharge from the pusher furnace the slabs land on a roller table which delivers them through a high-pressure water descaling box to the main approach table of the four-high plate mill. This table has alternate tapered rolls for slab turning and heavy side guards for centering.
Four High Plate Mill
The four-high plate mill is a single-stand reversing mill with four rolls 132 inches wide. The two 39-inch diameter work rolls are supported by two 60-inch diameter back-up rolls. Each work roll is driven by a directly coupled 5,000 horse-power electric motor.
The mill housings are of modern construction permitting greater reduction of the slabs, on each pass, and thus, with faster working and larger slab sizes, allowing greater output. High pressure water descaling sprays are used on both sides of the mill to ensure a good clean surface finish. The outgoing mill table is a duplicate of the working table except that the rolls are not tapered.
After rolling in the four-high mill the plate is delivered to the hot plate leveller which straightens out waves or other irregularities. The leveller is a slow-speed mill with back-up rolls and is capable of straightening any size of plate produced at Clydebridge.
The plates are then moved along racks to the cooling floor where they are again examined for defects, segregated according to thickness, and marked according to the customers' orders. Plates 5/8 inch thick and less are by-passed to the rotary shear line, while rectangular plates of ¾ inch thickness and over continue along the heavy shear line. Plates of irregular shape are lifted off and passed to a hand-operated shearing line.
A rotary shear line, which began operation during 1963, comprises a rotating double-head side trimming and slitting shear, capable of cutting plates up to 10 feet 6 inches wide and slitting plates up to half that width. The plates are passed to the end-cut shear, which cuts them to rectangular shapes of the required size, then to a weighing machine for checking that the dimensions are correct, and finally to the cold levelling machine. The plates are now ready for despatch.
Heat Treatment
The heat treatment plant consists of a normalising furnace, quenching press and tempering furnace. Those plates which require heat treatment are taken from the cooling bay by transfer bogies and fed into an 80-foot normalising oscillating roller hearth furnace fired by coke oven and blast furnace gas.
This furnace has a normal rated capacity of 8 tons per hour. Plates which are required to be hardened are passed from the output end of the furnace to a 60 feet x 11 feet 6 inch quenching press capable of taking plates up to 2 inches thick. The heat treated plates are then taken by transfer bogie to the cooling floor for marking and shearing by way of a levelling machine where the plates can be flattened if necessary, although most plates do not require to be flattened.
Should the plates require to be tempered they are treated in the 50-foot oscillating roller hearth tempering furnace fired with a mixture of coke oven and blast furnace gas. This furnace has a normal rated capacity of 6 tons per hour. After treatment the plates are delivered to the cooling floor for marking and shearing.
Ancillary Services
Shot Blasting & Priming Plant
Clydebridge Works is particularly well equipped for producing the high-quality steel plate required by modern structural and civil engineering. To meet the demands of the shipbuilders there is also a shot blasting and priming plant for the elimination of mill-scale. The plates are finally given a protective primary coating to inhibit corrosion and to serve as a base for the customer's own painting.
Special Equipment At Clydebridge
​
Closed circuit television is installed in control pulpits throughout the plant to keep an eye on the plates at critical points in the various processes.
​
Lamson tubes and Tannoy loud hailers are also used extensively at control points. The lamson tubes are particularly useful for transmitting written instructions from the production planning office to the control pulpits with the minimum of delay.
​
Internal rail traffic at Clydebridge, and also between Clydebridge and Clyde Iron Works, is handled by seven diesel locomotives.
There are over 60 electric cranes for essential lifting and transfer duties, particularly in the melting shops, and the slabs are handled by a fleet of heavy duty fork-lift trucks.
​
Water from the river Clyde is used in large quantities particularly in the melting shop where the furnace doors and lintels are water cooled
Computer
The Computer Centre sited adjacent to Clydebridge Works provides a service to all the Scottish works of the British Steel Corporation and also to General Steels Division Headquarters in Glasgow.
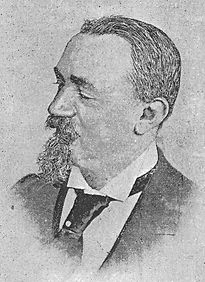